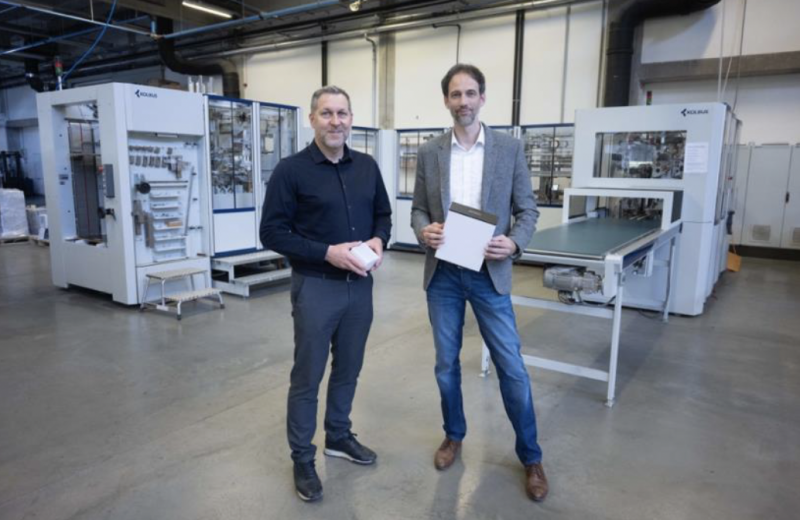
"Aki mer, az nyer" is what they say in Hungary, which means "nothing ventured, nothing gained". And so it is thanks to the entrepreneurial courage of the Keskeny family that their small commercial print shop has today become one of the most important printing companies in the country. Kolbus has also been a partner for some time now.
Keskeny was founded in Budapest in 1990 and renamed Keskeny & Co. after the turn of the millennium 2001. Today, the company employs 450 people and is the largest purely family-owned company in Hungary. It is led by CEO Arpad Keskeny, who was also instrumental in the decision to enter the packaging market with Keskeny. It started in 2004 with folding cartons and corrugated cardboard boxes for a wide range of applications, such as sweets, cosmetics, toys, convenience food, clothing and beverages. The success of this segment contributed decisively to the company's continued growth in the following years. This eventually encouraged Arpad Keskeny to expand his company's portfolio again, this time to include gift and luxury packaging made of wrapping cardboard.
Reliable gut feeling
"We entered the segment completely from scratch at the time," Keskeny recalls. "It was a purely intuitive decision without much market analysis." It was prompted by the realisation that there was no supplier for such boxes in Hungary at the time. So Keskeny decided to fill this gap: "We didn't even have any concrete inquiries from our clientele," says Arpad Keskeny, "but we had the feeling that this could be something." Initially, Keskeny started manufacturing with a machine from an Italian manufacturer. Completely without a sales organisation, the company approached its existing folding carton customers and informed them about the new offer. Keskeny found inspiration during a visit in 2016 to the Luxe Pack in Monaco, where, not entirely by chance, Kolbus was also represented and presented machine-produced packaging ideas. Kolbus was already benefiting from the experience gained over many decades of manufacturing machines for book production. "Cutting and wrapping cardboard for luxury packaging is similar to book cover production in many aspects," explains Henning Meier, Sales Director at Kolbus. "We used this know-how to open up new markets." Kolbus not only adapted its existing casemakers for cardboard box production, but also began to develop entirely new solutions, e.g., with new technologies for magnet insertion and wrapping, grooving, punching and forming.
The beginning of a partnership
"This was exactly the equipment we needed," says Arpad Keskeny, who was not only looking for innovative technology, but also for a way to produce smaller runs economically. The fact that Kolbus is an established European supplier that stands for high-quality machine construction and robust technology also inspired confidence. The discussions between Keskeny and the Kolbus team not only led to an investment in no less than three Kolbus machines - a casemaker, a magnet inserter and a grooving machine - but also resulted in an intensive partnership that continues to this day. "You can always reach a contact person at Kolbus. The team reacts quickly to requests for improvement and suggestions with suitable solutions," says Arpad Keskeny, citing another reason for this. With the new product, Keskeny continued his boom. Even without major advertising, the business almost ran by itself. Many customers who had previously ordered folding boxes now also ordered cardboard boxes. These are resellers, but also industrial customers from the gift, cosmetics, and technology sectors. The demand grew, and so Keskeny invested in Kolbus technology again in 2022.
The line becomes complete
The company expanded its machinery for box production in 2022 with a Box Line Taper BLT 200 and a Box Line Wrapper BLW 200. The taper is used to erect the cardboard blank and fix the sides with hot sealing tape. The resulting box is then wrapped and laminated on the wrapper. The wrapping is done using lateral forming plates instead of moulded blocks, which greatly simplifies format and job changes. With this special technique, the inner surfaces of the side panels can be wrapped right down to the bottom, which ensures a harmonious, high-quality overall impression. The Taper and Wrapper are the first machines worldwide that do not require the use of format-dependent moulding parts. These specially manufactured parts are expensive and must be normally ordered externally. The elimination therefore saves a lot of money and time. Arpad Keskeny currently sees the greatest potential in short runs. "Due to the tool-free adjustability without the need of moulded parts, the set-up time is very low. This lowers the fixed costs considerably," says Arpad Keskeny. "Nevertheless, the system is fast enough to handle long runs as well." Thus equipped, Keskeny is now planning to tackle the luxury and gift packaging business more aggressively. For the first time, an in-house sales department is to be set up for this purpose in order to attract new customers, and an online shop is also to be launched soon. Currently, an existing hall on the company's premises with 3200 square metres of floor space is being completely renovated. After completion, it should offer enough space to arrange the Kolbus machines involved in the box production into a line. This should enable continuous production without intermediate stops for loading and unloading. The goal is fully automated box production at Keskeny.
FLTR: Árpád Keskeny CEO, Keskeny and Partners Printing Co., Budapest, Hungary Henning Meier, Sales Director KOLBUS GmbH & Co. KG
Detail: Box with deep turning in up to the bottom