BX Motion Unveiled to North America
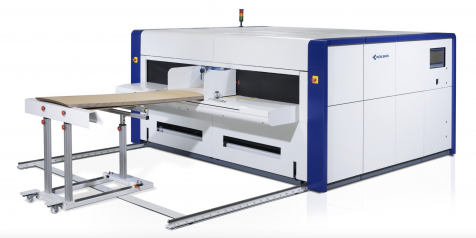
Designed from the ground up, utilizing both UK and German engineering design teams, it offers ground-breaking build quality and reliability. The new machine is flexible, taking stock sheets and cutting, creasing, slotting, digitally printing, and finally gluing the boxes, in one seamless process. The modular design of the BX Motion enables each machine to be precisely configured to individual customer’s requirements, even down to the sequence of processes. Customers can produce customized single, double, or triple wall boxes with selectable tool configurations, adapted to their specific production needs. Stock from E flute up to AAC triple wall can be processed, in sheet widths from 3.9" to 102.3", and lengths from 13" to 236.2".
This design provides the customer with options right from the point of feeding corrugated board into the machine. A simple trolley will facilitate manual feeding or the Autofeed AF300 can be specified for automated production. There is then a choice of creasing tools for corrugated board sheets from .2" to .6" thickness. A particularly innovative feature is the ability to produce up to three boxes of the same size and style, across the 102.3" width of the machine. The new slotting system enables a change time of less than five minutes as blades and tooling are prepared while the previous job is being run.
![]() |
![]() |
![]() |
Transport rollers and tools are positioned automatically according to FEFCO code and format, with automated adjustment of all creasing and cutting tools on the horizontal axis for precise positioning. Any waste board can be diverted downwards into shredders for recycling, production is uninterrupted by waste material passing through the machine. More than 50 FEFCO box styles can be produced.
Pneumatically controlled cross cutting is available plus automatically adjustable die cutting producing finger holes or contours with punching tools. The slotter has automated cross creasing with correction of creasing depths and a conveyor belt for waste. Inline Gluing can be specified, with an automatic nozzle gluer applying cold glue to selected areas. The BX Motion digital printing option offers a wide range of customisation making it perfect for any sheet plant, large or small, that requires short runs of individually designed boxes.
BX Motion sheer cut knives, for cutting to width BX Motion multi length slotting knives. Each singlecolor print unit has two heads and up to eight units can be used. They can be positioned individually or linked to produce one larger image. Resolution is 360dpi at speeds of up to 328 feet/minute, to the edge on both sides and within .78" of the head and foot.
Like every Autobox machine in the range, the BX Motion is equipped with the Copilot® system enabling the operator to control all the machine’s functions from one touch screen. Without tools, they can set up the machine automatically and program repeated adjustments. There is also access to the Remote Services Gateway, Kolbus 24-hour remote service back-up. With flexibility at its core, and modules which can be individually adapted to meet all requirements, the BX Motion allows users to customize their machine to their precise requirements.
First Order Already!
After the much anticipated product launch, Kolbus America celebrated its first order of the BX Motion to a North American customer, scheduled for installation later this year. The installation of this machine marks a turning point for the unnamed company, as they look forward to the BX Motion revolutionizing their shortrun boxmaking.
New Headquarters
In addition to consistently introducing innovative machinery to the corrugated industry, Kolbus has expanded its footprint across North America. While retaining its presence in Kalamazoo, MI, Kolbus America now operates its headquarters out of a new office in Huntersville, NC, conveniently located near RD 115S reference partner, CompanyBox. The company has also invested in hiring top talent from the local Charlotte area, including a full financial team and office manager. They’ve also increased their number of service technicians to best serve customers across the US and Canada.
Kolbus customers purchase with confidence knowing that Kolbus products are backed by a 250-year reputation for reliability and a service team that’s prepared to assist on site or remotely 24 hours a day. “I can’t say enough good things about the Kolbus team,” said Mike Seifert of Opus Packaging. “The availability of parts is fantastic. We’re usually able to get emergency parts overnighted, so production isn’t affected. Their support has been excellent, and we’ve been happy with their training team. What sets them apart is having a quick and free 24/7 online support, which gives us peace of mind. Overall, my experience with Kolbus has been terrific and I would highly recommend this machine to anyone looking for new equipment.